As a fashion design major at Liberty University, Luis Quijano doesn’t just design clothes, he grows the fabric. To do so, he ferments a mixture of water, sugar, green tea and kombucha, which creates a material that resembles leather called bacterial cellulose.
The textile can then be sewn together and used as fabric for clothing, though Quijano is only in the early stages of producing garments with his work. While he began fermenting the material in his dorm room, Quijano is now partnered with Liberty’s Department of Biology and Chemistry and uses the Center for Natural Sciences’ incubators to grow larger batches of bacterial cellulose.
By creating a natural, cruelty-free fabric that mirrors leather, Quijano plans to restructure the fashion industry by initiating a sustainable and equitable field of business. He plans to continue his research and design after he graduates in the spring, but before then, he plans to develop a few articles of clothing using the bacterial cellulose for Liberty’s 12th Annual Fashion Show. Until then, Quijano will continue tweaking his textile recipe to make it as affordable and attractive as he can.
Leslie Currie: What inspired you to pursue a career in fashion?
Luis Quijano: My first year I was actually a political science/pre-law major, and I switched to fashion design. Ironically, I felt like I could make more of an impact in the world through the fashion industry. I also liked how it was always changing; there are always new, innovative things to look at.
The people in the political science route weren’t people I could see myself being around for four years. There’s just a lot of corruption, and I didn’t want to be around that for my entire college career. I felt that there was more opportunity for me to make a difference in the fashion industry. It’s an international industry—it’s very big—so there’s more that I can do there.
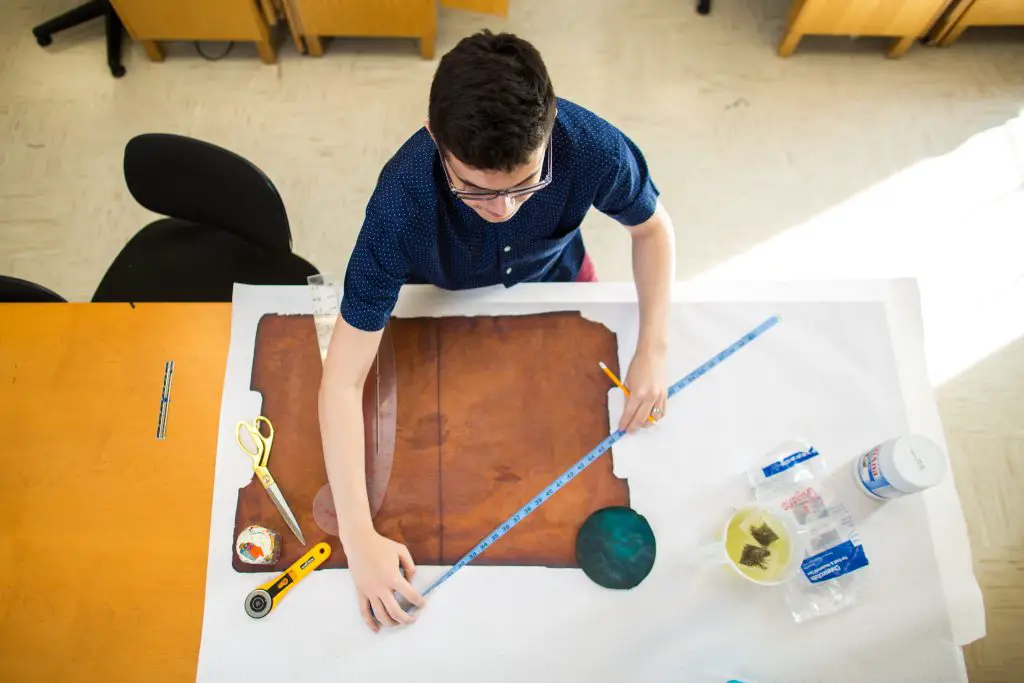
LC: Did any specific fashion designers inspire you to switch to the fashion industry?
LQ: To be honest, I didn’t know that much about fashion when I switched my major. At the time, I didn’t even know how to sew anything until I started. It was a sort of new deal for me. I mean, people complimented my style growing up, but I didn’t really know much other than the fact that fashion is always changing. After seeing some of the classes at Liberty, I was really interested and wanted to learn more. So that, in a way, guided me toward this major.
LC: You mentioned that you want to make an impact with fashion. How do you plan on doing that?
LQ: I’ve come across a statistic a lot, which is that the fashion industry is the second dirtiest industry in the world, behind only oil. According to the World Bank, textile dying alone accounts for 17-20 percent of all global industrial water pollution. So, a lot of people don’t realize that the clothing that everyone wears actually has a significant environmental impact. That’s where I want to make a change: How can I make clothing affordable but also sustainable and more ecologically friendly?
There’s always been the buzzword “sustainability,” even though people don’t always take into account why it’s a buzzword. Why is sustainability even necessary? What practices are industries using that make sustainability necessary? It seems like no one is actually going to make a change in these dirty business sectors.
So, I want to raise awareness, for instance, of the chemicals that are used by the fashion industry and the underpaid and abused textile workers that aren’t always heard. There have to be alternatives to these practices, which is one of the reasons why I really like this leather-like material I’ve been working on, bacterial cellulose. It presents an alternative to the pollution and chemicals. That’s one reason why I decided to research it.
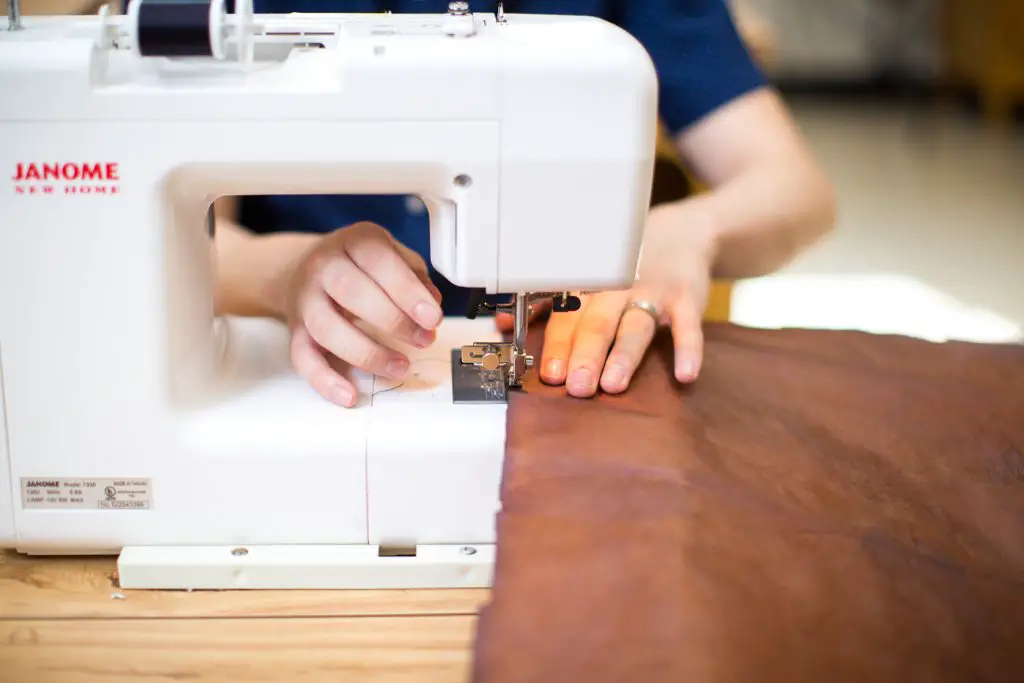
LC: You first heard of bacterial cellulose while watching a Ted Talk. How did you decide to try making the material?
LQ: I’m on the forensic speech team at my school and I needed a topic to speak about. Then I remembered a Ted Talk I had seen a while back. So, I found it—it was the Suzanne Lee Ted Talk, “How to Grow Your Own Clothes,” which I highly recommend watching. The topic is pretty abstract, but her Ted Talk addresses everything clearly. It was my sophomore year that I chose bacterial cellulose as my topic to speak about for a few of my speeches.
Then, during my junior year, I had to start doing semester projects for my fashion design major. I decided that for one of my projects, in my textile class that fall semester, I would try growing my own clothes. After doing speeches about the issue, it piqued my curiosity. I figured if I wasn’t able to physically grow the material, then I would write a paper about why I failed. It was a win-win, because either way I had a project. And then I ended up actually growing it! From there, it’s just been onward.
LC: How many tries did it take you to actually produce the textile?
LQ: Honestly, there isn’t much research online that tells you how to grow your own bacterial cellulose. Even then, I wasn’t sure what tea to use or anything specific. I had to really do my own research. I searched online and learned what I could by talking to other people who had heard of it. It took me that whole semester to figure out how to grow the fabric.
Toward the end of the semester I finally started growing it successfully. So, I know how to grow it on my own now, but every single time you grow it the textile can end up looking completely different from the last batch. There isn’t one pattern or marking that always occurs, which can be a cool thing. It’s like leather in the sense that every hide is different in some way. Each has its own distinct look.
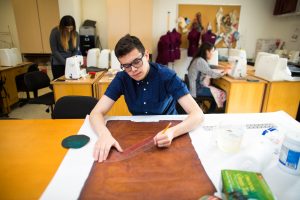
LC: What kinds of garments can you use it for?
LQ: Well, I haven’t created anything yet. I’ve only just started growing it. But in April, Liberty hosts its annual fashion show, and I plan on making at least three garments just using this product. So, I’m starting to prepare for that event. Each batch takes about three weeks to a month to grow, and I need enough fabric to make everything. I guess it’s a little crazy because it’s not a small project in the slightest. My first design project with this material is going to be a very huge one—we’ll see how it goes!
LC: So you have the annual fashion show in the spring, and you graduate as well, right? What are your plans after graduation?
LQ: Yeah, commencement will be in the spring, which is pretty crazy. But I actually just applied for the Fulbright Student Program, which is a grant program that would allow me to travel abroad and work with foreign schools to cultivate my studies on this project. So if I get that, I’ll start my doctorate right after I graduate; I would bypass my master’s.
I just plan on developing—whether I study in the United States or abroad—this material through graduate school. For instance, bacterial cellulose is not waterproof. It doesn’t retain moisture well because of the fact that it isn’t waterproof when it’s dry. So, I want to try to find ways to solve that issue. I also want to find ways to make this textile a commercial practicality, where clothing companies could use the fabric affordably. Those are my next steps, I hope.
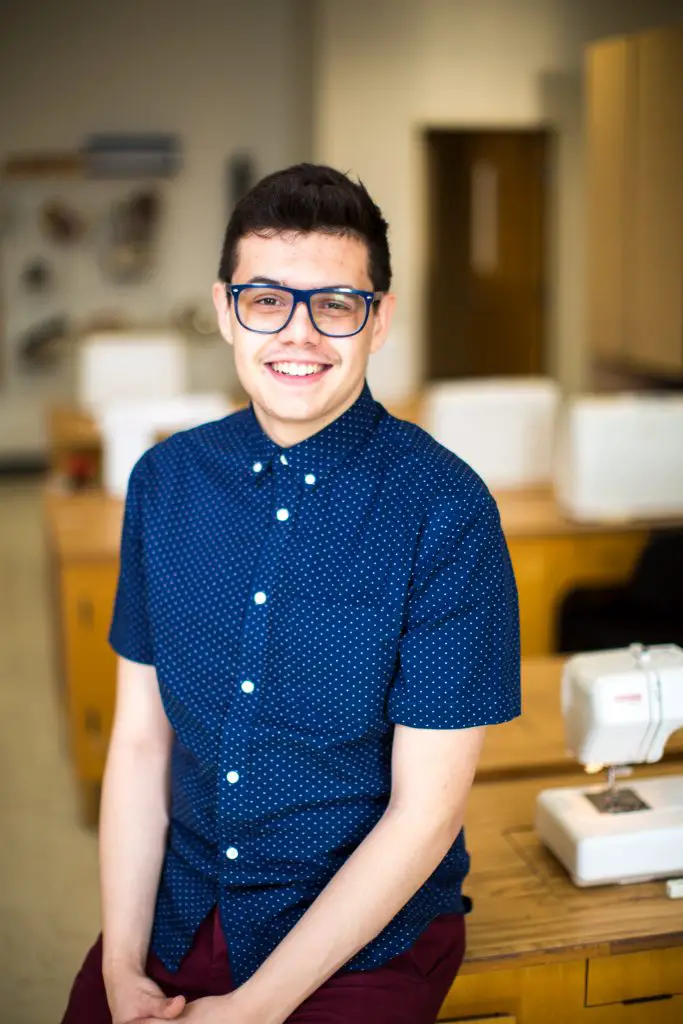
LC: Is the textile expensive to make?
LQ: Well, anyone can grow it on their own at home if they have water, sugar, green tea and kombucha tea. They would just need some sort of breathable fabric to cover the container while it ferments for three weeks to a month. I will say, though, that I think the most expensive part of creating bacterial cellulose on a large scale is having the space to store all of the materials, which comes down to the bin itself.
I’m also trying to find the cheapest sugar that is still effective in the fermentation process, but finding a bin that fits everything that’s needed is the most costly part. The fabric grows to the size of the container. So, if you have a really big container, say nine feet by nine feet, the fabric will be nine feet by nine feet in size. Something that would increase efficiency would be designing something where multiple layers of the fabric could grow on top of each other, or finding ways to stack the containers so that space is used more effectively.
I know it’s a little abstract. But, for example, with a woven fabric like cotton, the fibers are converted into yarn, which is then converted into the fabric. That cloth is then dyed the preferred color and cut into the correct shapes and sizes. Once cut, the material is sewn into garment, which requires some finishing touches, as well. With this material—bacterial cellulose—the fabric is grown.
It develops from the first four ingredients all the way into the finished product, almost. It just needs to be cut and sewn. In the future, we might be able to make containers that are already formed as specific pattern pieces, such as an arm sleeve, so that the extra step of cutting the material is circumvented. It would streamline the entire process from fermentation to sewing so that certain steps would be sidestepped.
LC: Can you dye the fabric? Does it work essentially like any other textile?
LQ: Yes! Bacterial cellulose is actually very color receptive. Most of the clothing that shows up if you search the material online is some shade of brown, but for the fashion show, I really want to dye everything. I want to focus on the color potential of this fabric because it definitely has that capacity. I’m starting to plan what I want to design for the show in April.
Because the fabric is a bit more rigid than a lot of other materials, it doesn’t drape well, so I won’t make flowy clothing. My designs are going to be more simplistic with sharp edges. I want the fabric to speak for itself rather than doing too much and overpowering it. I also want to the color of the dye to pop because the fabric dyes so beautifully. It’s unlike any other textile I’ve worked with. I’m pretty excited to see how it’s going to turn out.